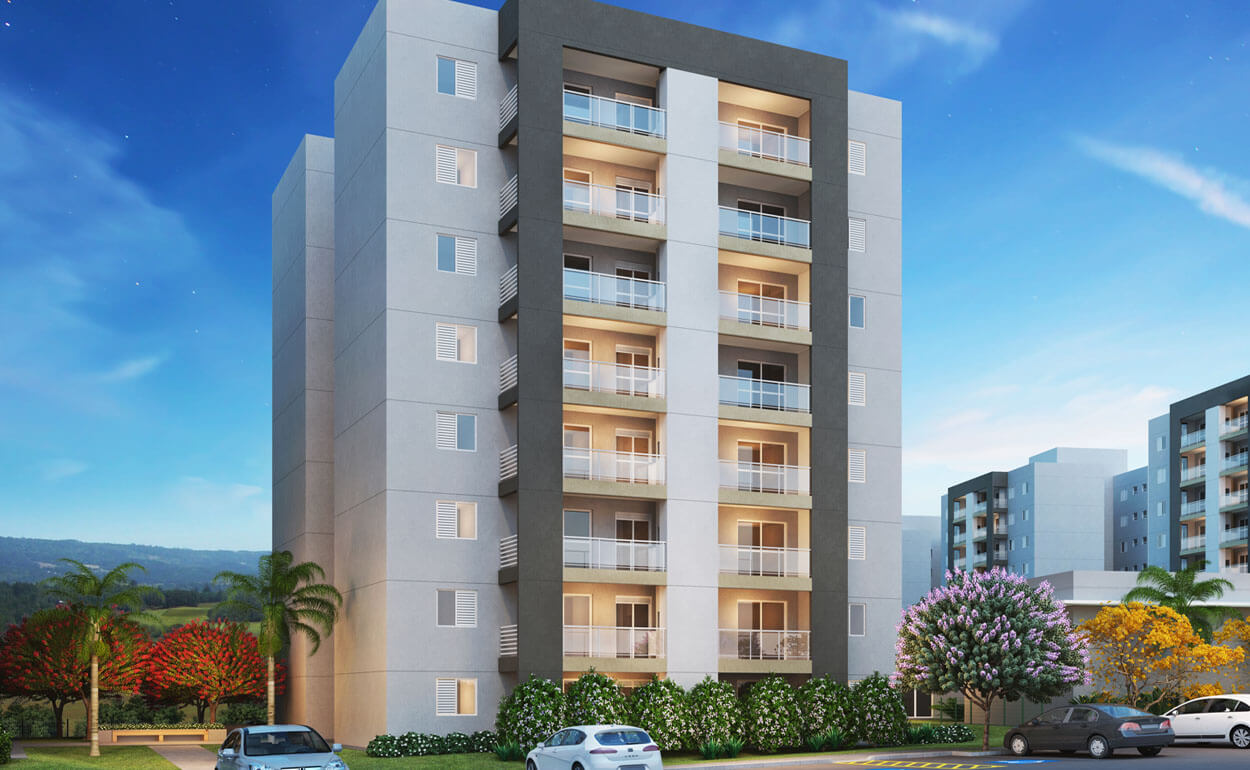
APLICAÇÃO DE FERRAMENTA LEAN MELHORA EM 19% A PRODUTIVIDADE EM PAREDES DE CONCRETO MOLDADAS IN LOCO E REDUZ CRONOGRAMA
O Condomínio Brisa da Mata 3 está localizado na cidade de Paulínia, interior de São Paulo. O empreendimento possui 14 torres de 8 pavimentos, com 448 Unidades Habitacionais, comtempladas em 2 tipos de plantas: apartamentos de 3 dormitórios (80,07 m²) e apartamentos de 2 dormitórios (60,66 m²), executados no método construtivo de parede de concreto moldada in loco.
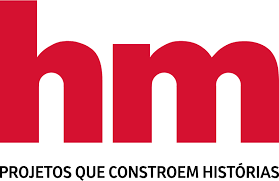
Solução técnica implementada
O empreendimento Brisa da Mata 3 foi escolhido como obra piloto para a implantação do Lean Construction na HM. Durante a etapa de inserção das ferramentas de planejamento e gestão da produção (Takt e Last Planner System), evidenciou-se uma necessidade na realização de um trabalho mais estruturado a fim de alcançar maior eficiência na execução das concretagens para garantia do atendimento dos prazos.
Na etapa de mapeamento do estado atual, verificou-se que 74% das concretagens iniciavam após às 16h, sendo que 63% destas concretagens não atingiam resistência no dia seguinte até às 6h30 da manhã, condição que impossibilitava as concretagens diárias, o que é extremamente crítico se tratando deste sistema construtivo.
Nos dias em que o concreto não atingia a resistência após às 7h30, cerca de 57% das concretagens diárias eram impactadas devido aos atrasos no processo.
Durante o processo, seguindo a tendencia que estava sendo observada na obra, foi mapeado que, do total de 164 concretagens previstas de ocorrer até o final da obra, 120 teriam um risco de iniciarem atrasadas e, destas, 45% teriam o risco de não ocorrer no dia programado, caso as melhorias não fossem implantadas.
A situação descrita acima resultava em inúmeros problemas para a HM Engenharia e para os empreiteiros responsáveis pela atividade, tendo em vista que os custos diários de perder uma concretagem eram consideráveis dentro do orçamento da obra e impactava diretamente em atrasos no cronograma, de até 27 dias úteis.
Em parceria com a consultoria Alvarez e Marsal, durante a implantação do Lean, foi utilizado o PCV (Plano de Captura de Valor), que é um programa utilizado para estruturar e gerir ações de melhoria na organização. A ferramenta auxilia no acompanhamento de ideias desde o momento da sua geração até a captura do resultado.
Como uma das iniciativas resultantes desse programa, realizou-se um workshop de produtividade para o método construtivo de Parede de Concreto moldado in loco.
A metodologia utilizada consistiu na realização de um workshop de 7 fases, embasado no pensamento A3, processo onde todos da empresa aprendem, desenvolvem os seus talentos, são capacitados para identificar as causas raiz de um problema e a propor soluções práticas e eficientes, contemplando todas as etapas necessárias para melhoria de um serviço ou atividade.
Ao realizar cronoanálise de todas as atividades envolvidas na execução da Parede de Concreto, foi possível classificar aquelas que agregam valor ao produto, desperdícios ocultos e desperdícios evidentes, sendo possível realizar o mapeamento do estado atual do processo. Com essas informações em mãos e com base no processo atual, em conjunto com a equipe multidisciplinar presente durante o Workshop, utilizou-se a ferramenta de FCA (Fato, Causa e Ação) para cada um dos desvios mapeados como desperdício do processo. Foram implantadas todas as ações de correção propostas, além de realizarem o novo desenho do processo com os ajustes. As análises foram realizadas novamente para aferir os ganhos no tempo de ciclo. Dentre as principais ações de correção no processo, destacam-se:
- Alteração no processo construtivo: liberação da montagem da armação das paredes internas no 1º horário do período da manhã (antecipando 60% do trabalho que seria realizado na parte da tarde);
- Implantação do dispositivo para agilizar o içamento das telas;
- Implantação da central de corte de telas.
Com essas alterações realizadas, realizou-se uma nova cronoanálise para nalisar os ganhos de produtividade.
Principais resultados obtidos
Na cronoanálise, medimos o tempo de cada processo, identificamos as oportunidades, implantamos as melhorias e depois medimos novamente para avaliar o ganho de produtividade.
Durante a fase piloto foram implementadas e testadas as melhorias propostas pela equipe, o que resultou em ganhos de produtividade por meio da redução de cerca de 2h (19%) no tempo de ciclo diário do processo, gerando aumento na eficiência das concretagens.
Potencial de redução de custo total de R$ 320.000,00, sendo estes R$ 200.000,00 de custo indireto (redução de hora extra de toda equipe devido a redução do tempo de ciclo do processo e redução de 27 dias úteis do cronograma da atividade com o aumento na eficiência das concretagens diárias) e R$ 120.000,00 de custos diretos devido redução de custos de locação de equipamentos, hospedagem da equipe de forma e alimentação.
Com a alteração no processo construtivo, conseguimos liberar a montagem da armação das paredes internas para o 1º horário do período da manhã, antecipando 60% do trabalho que seria realizado na parte da tarde.
O processo de concretagem anterior resultaria num impacto de até 27 dias úteis de atraso no final da obra. Com as alterações conseguimos evitar esse atraso, gerando economia e produtividade na obra.
Tivemos redução de hora extra de toda equipe devido a redução do tempo de ciclo do processo e redução quase um mês do cronograma da atividade com o aumento na eficiência das concretagens diárias. Além disso, houve redução de hospedagem da equipe e alimentação, já que passaram menos tempo em campo.
Tivemos também redução dos esforços da equipe, devido a redução da duração do tempo de ciclo do processo, impactando diretamente a jornada de trabalho dos operadores;
Redução dos riscos operacionais da atividade, tendo em vista que o início ocorre antes do anoitecer.
Diminuição de desperdícios ocultos e desperdícios evidentes.
Com o novo processo de montagem de armação e a implantação de novas metodologias, tivemos ganhos de qualidade e organização do processo.
Qualquer empreendimento que possua o sistema construtivo de Parede de Concreto Moldada In Loco.
Para reproduzir esta metodologia em outros empreendimentos recomenda-se:
- Treinamento das equipes envolvidas;
- Alinhamento das interfaces com as equipes de Segurança do Trabalho e Qualidade;
- Revisão dos procedimentos e Instruções de Trabalho.
- Conferência diária de acordo com os procedimentos padrão.
Implantação da cultura de análise de desperdícios e melhoria contínua dos processos.
Parceiros envolvidos
Alvarez & Marsal | HM Engenharia
Nathally Dias Macedo - Excelência Operacional
Leandro de Castro Melo - Diretor Executivo de Engenharia
Leandro de Castro Melo - Diretor Executivo de Engenharia
https://eme.maishm.com.br/imoveis/brisa-da-mata-manacas