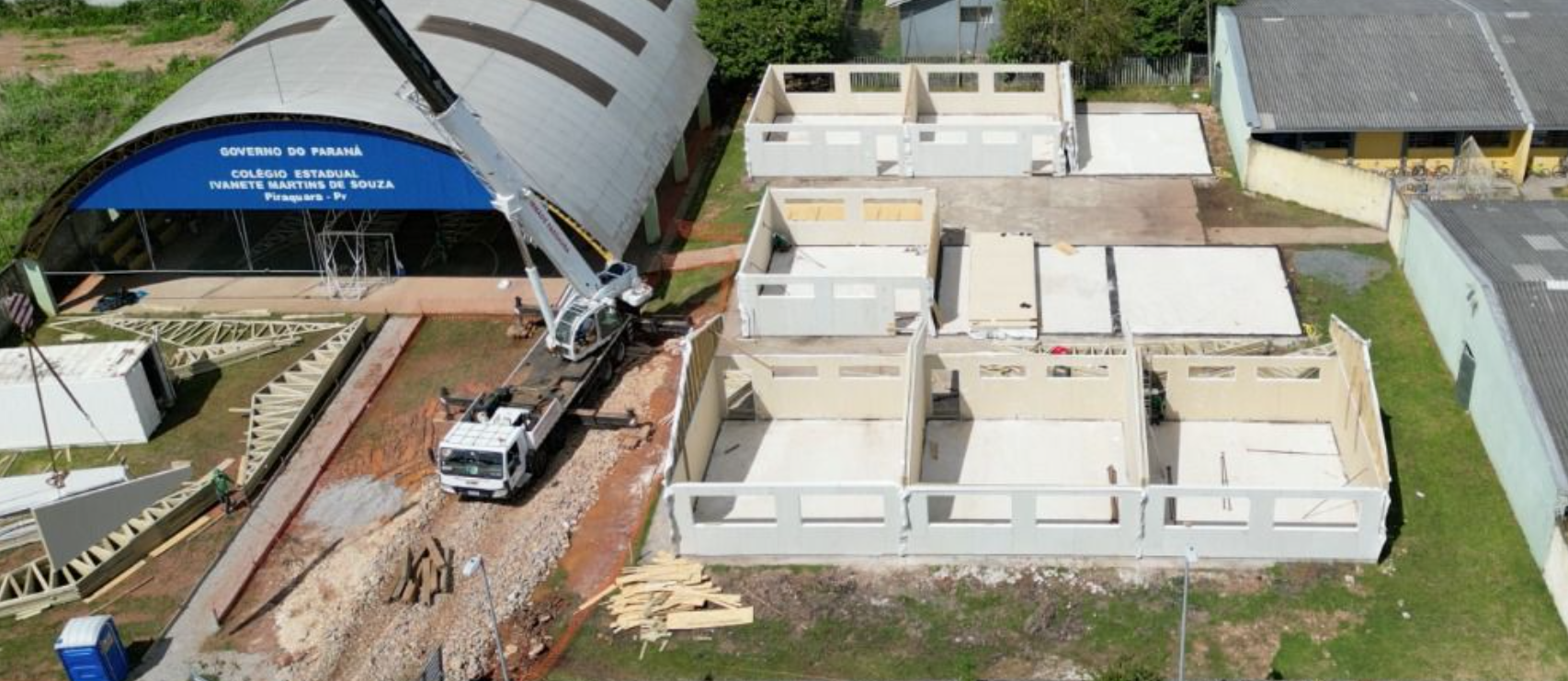
Impacto na obra
SISTEMA INDUSTRIALIZADO AGILIZA EM 4x O PRAZO DE ENTREGA DE 321 SALAS DE AULA EM LICITAÇÃO NO PARANÁ
Com o sistema de construção industrializada off-site, o projeto de renovação de salas de aula das escolas no Estado do Paraná contou com escalabilidade e vários endereços atendidos. Contemplando mais de 321 salas entregues e substituição de ambientes por salas amplas, iluminadas e termoacústicas, o projeto trata-se de uma ampla operação em regime de força tarefa, que demanda a remoção e substituição de salas com o menor impacto possível na operação das escolas.
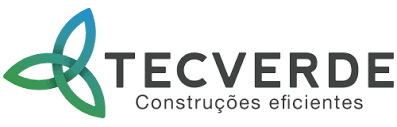
Solução técnica implementada
O Governo do Estado do Paraná lançou em 2022 um edital com o objetivo de contratar uma empresa que fosse capaz de executar, em 18 meses, 400 salas de aula com sistema ecológico e sustentável, que trouxesse maior conforto térmico e acústico aos alunos e professores.
O escopo era de realizar a implantação de salas de aula completas (desde a fundação até a entrega final, incluindo quadro negro e acessórios). Cada sala de aula conta com a capacidade para 35 alunos e, ao total, serão 400 salas implantadas, com entrega de 1 unidade/dia.
O equipamento escolar demandava atualização e ampliação, o que seria dificilmente amparado com soluções convencionais de execução. Além disso, o setor público necessitava de profissionais para acompanhar em vários de endereços e em obras longas, fato que poderia impactar na gestão.
Foi aplicado o processo de construção industrializado, com uso de sistema pré-fabricado de painéis em Light Wood Frame. Os revestimentos internos e externos (gesso e placas cimentícias), esquadrias e vedações, instalações elétricas e estrutura de cobertura foram executados com processos aplicados em fábrica.
Para desenvolvimento do projeto, contamos com o apoio da equipe de engenharia, utilizando tecnologia e metodologia BIM e conceitos Lean, otimizando os processos envolvidos e potencializando a industrialização da obra em ambiente off-site/industrial.
Esse projeto foi 100% desenvolvido internamente por equipes próprias, bibliotecas de produto padrão com soluções específicas, que adicionaram velocidade na produção e montagem das estruturas.
Foram desenvolvidos elementos de quebra de cantos, sobreposições planejadas de chapas, padronização e pré-corte de elementos de cobertura, paginação de chapas de paredes, forros, revestimentos cerâmicos e listas sequenciadas de corte de matéria prima, transformando a obra e a fábrica em linhas de montagem, com pouco ou em alguns casos nenhuma preparação de materiais para aplicação.
Após todo o desenvolvimento, foi realizado um workshop com as áreas de Produto, Processos, Operações e PDI, a fim de extrairmos mais oportunidades de desenvolvimento, o que potencializou o resultado do projeto.
No projeto, além de criar uma estrutura enxuta, foram adotados critérios de padronização, a fim de reduzir as etapas de fabricação e montagem. Em diversos escopos optou-se por simplificação e padronização, trazendo flexibilidade e velocidade nas etapas operacionais. Como exemplo, na execução das paredes de geminação, ao invés da utilização de um painel de 21cm de largura, como era padronizado (o que geraria um painel específico em relação aos demais), aumentamos para 2 painéis de 14cm. Esta alteração supera o desempenho demandado, mas permite grande simplificação de fabricação, redução de etapas, da lista de materiais e aumento da produtividade nesta fase.
Em canteiro, foi criado um sequenciamento de atividades em quatro grupos multidisciplinares: Fundações, Montagem, Revestimentos e Pinturas, com um intervalo reduzido de prazo de entrada entre grupos. Neste caso todas as etapas foram vencidas por esses quatro grupos sintonizados, gerando um paralelismo das linhas de avanço, tornando-as controláveis e com poucos interlocutores e interfaces, possibilitando uma compressão do cronograma de até 14 dias. As medições de produtividade foram realizadas diariamente através de cronoanálise.
Principais resultados obtidos
O emprego destas soluções trouxe uma redução de prazo de cerca de 75% em comparação com os principais sistemas construtivos tradicionais, além da redução de mão de obra.
Utilizando revestimentos já aplicados nos painéis em ambiente fabril, foi possível atingir um Takt de 1,5 salas montadas (com telhas e esquadrias) por dia, com uma equipe de montagem de 7 pessoas.
Com a produção de kits elétricos já embutidos nos painéis, a parte elétrica de uma sala era executada em 30 min por um colaborador sem conhecimento específico, o que normalmente seria realizado em quase 1 dia por sala com mão-de-obra
A otimização e a celeridade dos serviços possibilitaram a redução com custos indiretos de canteiro, pois demandou menos tempo em campo da equipe administrativa de obra e de acompanhamento. Ou seja, foram usadas estruturas de apoio mais simples e obteve-se menos custos com deslocamentos de equipe e com alimentação.
Por se tratar de um produto industrializado, com otimização e redução de desperdícios, foi possível garantir uma obra sem aditivos e sem surpresas financeiras provenientes da falta de planejamento. Houve também grande redução dos riscos de segurança do trabalho, visto que boa parte das estruturas é executada em ambiente controlado.
Com isto, reduz-se em 4x os custos indiretos de obra, em comparação com a construção convencional em alvenaria. Sem considerar a drástica redução de custos para a máquina pública, principalmente na questão de medição das obras, que passaram a ocorrer uma única vez em cada obra, e não mais mensalmente.
Industrializar a obra impacta em todos os subsistemas, além do sistema construtivo se demostrar mais produtivo por si só, o uso de equipamentos mecânicos na produção eleva este parâmetro. O subsistema que maior sofreu impacto foi o de instalações elétricas, onde utilizou-se kits pré-fabricados embutidos nos painéis, com os módulos de tomadas e interruptores instalados. Para as luminárias foram utilizados kits elétricos soltos, instalados por qualquer colaborador, ou seja, eliminou-se a mão-de-obra especializada.
Com isso, o processo de instalação foi de 30min por sala, ao invés um dia inteiro
Com sistemas construtivos tradicionais a expectativa seria 6 meses (180d) de obra, considerando-se a média de colaboradores. Através de relatos da contratante, notou-se que frequentemente ocorriam descumprimentos dos prazos pré-estipulados, uma vez que ampliações são complexas com a escola em operação.
Já com a adoção do sistema industrializado da Tecverde, o período de obra caiu para 1,5 meses (45d), ou seja, quatro vezes mais rápido que os sistemas convencionais.
As equipes foram separadas em 4 grupos, que executam seus serviços em ciclos semanais e passam para o próximo passo da implantação:
Fundações: 5 pessoas – 2 semanas; Montagem e vedações : 7 pessoas – 1 semanas; Revestimentos e acessórios: 3 pessoas – 1 semanas; Pinturas: 6 pessoas – 1 semanas; Checklist: Gestor do contrato – 1 semana
De acordo com dados da Tabela de Composições e Preços para Orçamentos (TCPO), a estimativa de pessoas no canteiro, mantendo o mesmo cronograma, ficaria de 5 a 8 vezes maior do que no sistema industrializado.
Para o Estado e a população, foi possível entregar atendimento simples e eficaz de uma demanda represada por ambientes de ensino, já que as vagas escolares estavam em falta. Uma contratação convencional levaria anos para resolver esta questão.
Além disso, o sistema construtivo resultou em outros pontos positivos, como:
Obra mais limpa e organizada; Redução de 85% dos resíduos em obra; Construção 4x mais rápida; Economia de 90% em recursos hídricos; Conforto térmico e isolamento acústico; e Redução do risco de acidentes de trabalho durante a execução da obra.
Com a utilização do sistema construtivo industrializado da Tecverde Engenharia, percebemos uma melhora substancial em todos os parâmetros, entre os que mais se destacaram foram:
Redução do tempo de obra; menor impacto dentro das escolas em relação a tempo de obra e segurança dos alunos e professores; redução de custos indiretos do contratante e da contratada; redução de colaboradores em obra, assim como acidentes de trabalho.
Em relação ao produto, entregamos uma maior eficiência termo-acústica, melhor qualidade geral do ambiente, aumento da capacidade de dispensação de vapores e umidades, eliminação da condensação nas esquadrias e melhoria na ventilação e iluminação.
Obras corporativas como: Alojamentos, hospitais, escolas, edifícios e centros comerciais, edificações de apoio para concessionárias viárias, lojas e franquias e obras residenciais como casas térreas, sobrados e prédios até 4 pavimentos.
Trata-se de um Sistema Construtivo de alta tecnologia, que conta com até 85% das etapas alocadas em fábrica, com controle de qualidade e eficiência do produto. Todos os materiais são aprovados pelo Programa Setorial da Qualidade que certifica insumos para a construção, atestando sua qualidade e o seu desenvolvimento tecnológico. A inspeção de qualidade deve ser realizada no início da produção e durante toda a obra, diretamente no canteiro. Os critérios técnicos no desenvolvimento de soluções de impermeabilização, vedação de esquadrias, coberturas e dimensionamento dos fixadores são essenciais
Atualmente temos em andamento diversos estudos para melhoria de produtividade nas linhas de fixações, processos de montagem, linha de produção, sistemas elétricos e revestimentos.
Algumas salas já estão sendo produzidas com a linha de fabricação de paredes na vertical, o que gera paralelismo de processos na face interna e externa dos painéis (até então nossa linha produzia painéis na horizontal).
Para futuras implantações a Tecverde estuda a produção de módulos de cobertura industrializados com telhas instaladas em fábrica, que garantirão redução em até 4 dias por cada 3 salas de aula montadas
Parceiros envolvidos
Frametec – Mão de obra para construção à seco | Isoeste – Telhas termoacústicas | Gypsum – Placas de gesso acartonado e cimentícias
Felipe dos Santos Basso – Diretor de Negócios Corporativos
Beatriz Modesto Fróes – Analista de Novos Negócios
Gustavo Henrique – Coordenador de Contrato
José Antônio Bento dos Santos – Assistente de Engenharia
Allan Michel de Oliveira Sousa – Orçamentista do projeto
Pedro Virmond Moreira – Sócio fundador e Diretor de Engenharia de Produto
Caio Bonatto – Sócio fundador e membro do conselho.
Beatriz Modesto Fróes – Analista de Novos Negócios
Gustavo Henrique – Coordenador de Contrato
José Antônio Bento dos Santos – Assistente de Engenharia
Allan Michel de Oliveira Sousa – Orçamentista do projeto
Pedro Virmond Moreira – Sócio fundador e Diretor de Engenharia de Produto
Caio Bonatto – Sócio fundador e membro do conselho.
https://www.tecverde.com.br/ , https://www.tecverde.com.br/nossas-obras/ , https://www.tecverde.com.br/sistema-construtivo/ , https://www.linkedin.com/company/tecverde-engenharia-ltda/mycompany/ , https://www.instagram.com/reel/Cp5I_pFgS9p/?igshid=MDJmNzVkMjY=