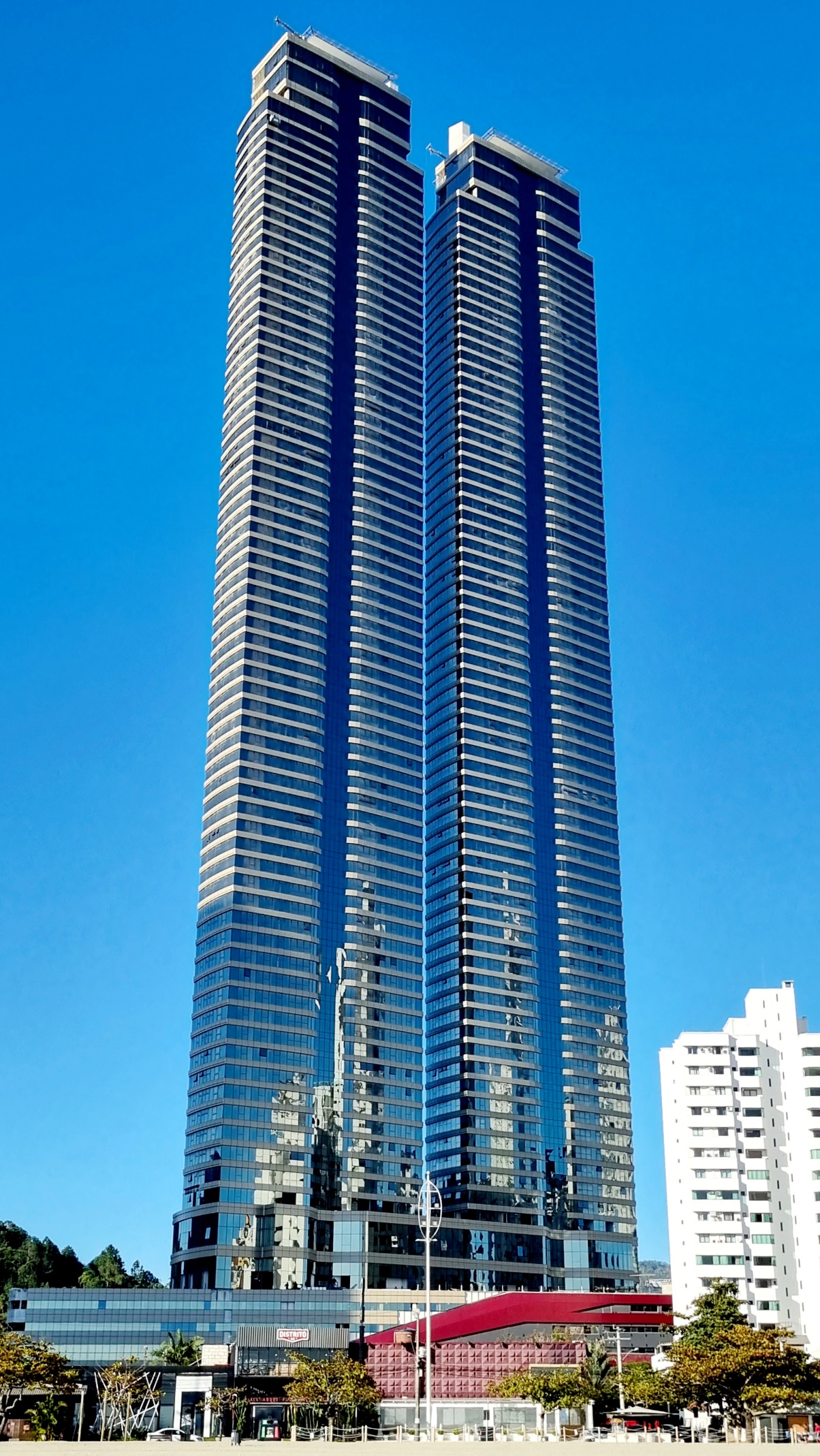
YACHTHOUSE BY PININFARINA: SISTEMA DE INSTALAÇÃO DE FACHADAS REDUZ EM ATÉ 73 DIAS O PRAZO FINAL DA OBRA
O projeto Yachthouse by Pininfarina foi concretizado pela parceria entre Pasqualotto & GT.
Composta por duas torres com 281 metros de altura e 81 pavimentos, é uma obra única no Brasil.
Por sua grandiosidade, se tornou um grande desafio para todos os envolvidos a sua realização.
Ao Consórcio CLN foi destinado o desafio de produzir e instalar toda a fachada unitizada em todo o perímetro do empreendimento.

Solução técnica implementada
Normalmente os painéis que compõem uma fachada unitizada são produzidos e montados dentro da fábrica, carregados por caminhão até a obra, descarregados, movimentados e, por fim, instalados. Porém essa solução se tornou inviável no empreendimento Yachthouse.
O projeto demandava painéis personalizados e, para atender o cronograma, era necessária à produção média de 60 painéis por dia. Pela complexidade do empreendimento, havia também desafios no planejamento e logística.
Para viabilizar a execução da fachada no prazo solicitado pelo cliente uma série de inovações foram criadas e adaptadas, desde a produção dos painéis em outro estado, a montagem e colagem dentro da própria obra, a movimentação vertical dos painéis, até a sua instalação nos pavimentos, para assim entregar aos contratantes um projeto de excelência, compatível com a grandeza do empreendimento.
As soluções apresentadas foram criadas e definidas pelo Consórcio CLN. Para que algumas etapas fossem realizadas dentro da obra, nossos fornecedores também tiveram que se adaptar a essas mudanças.
Os perfis e acessórios foram preparados na fábrica da Luxalum. Nessa etapa o corte e usinagem são realizados e os kits de painéis são acondicionados em pacotes individuais. Cada kit é composto pelos perfis e acessórios necessários para montar um painel. Com os kits de painéis prontos e identificados, as cargas são montadas para carregar o caminhão com destino ao Yachthouse.
Para agilizar a etapa de carregamento e descarregamento em obra os painéis foram montados em paletes, sendo amarrados e lacrados.
Outra atividade que foi implementada especificamente nesta obra foi a montagem das caixas de ACM, da mesma forma que os painéis. As chapas foram cortadas e acondicionadas em paletes juntamente com suas estruturas.
A montagem foi realizada em um setor separado no piso G5 (garagem) por uma equipe terceirizada dedicada. Dessa forma, eliminamos os danos causados no transporte e reduzimos o volume útil de carga em cada caminhão.
A primeira medida tomada foi a divisão da montagem dos painéis em duas etapas, sendo o corte e usinagem realizados na fábrica da Luxalum e a montagem e colagem dos vidros e ACM na obra.
Foi criada uma fábrica completa dentro da obra para alcançar a produção diária de 60 painéis. Demarcamos uma área junto ao cliente e montamos a linha de produção, cada setor foi definido e demarcado, como o administrativo, almoxarifado, estoque de kits de painéis, montagem etc.
A maior dificuldade desse projeto foi produzir e levar os painéis todos os dias para o local de instalação, pois são 81 pavimentos e duas torres iguais. A logística para o transporte foi inovadora, equipamentos e procedimentos foram criados para atender cada etapa.
Por exemplo, criamos o carrinho linha para transportar os painéis da linha de produção, onde havia um trecho com trilhos e estrutura em forma de carrinho para que os painéis pudessem ser retirados da linha de produção e levados para qualquer área da fábrica.
Para medir a produtividade, diariamente a produção e instalação dos painéis eram registradas em planilha de controle e compartilhada mensalmente com o construtor, dessa forma ambos acompanham a produção real.
Principais resultados obtidos
Estima-se que adotando o método tradicional, onde os painéis de fachada fossem fabricados, montados e colados em uma fábrica externa e sendo transportados por caminhões até o seu destino, a produção máxima com o mesmo efetivo de colaboradores seria de 45 painéis por dia, aumentando o prazo de execução em 24,98%.
Além do acréscimo no tempo de execução, a logística com transporte de painéis seria altamente afetada, tendo um crescimento de 84,69%. Onde antes tínhamos uma entrega por semana, passamos a ter 5 entregas.
A fábrica criada dentro da obra propiciou principalmente redução de custos na logística de transporte de materiais e redução no tempo gasto para a sua produção e instalação.
Com a montagem dos painéis na obra foi necessária a entrega de um caminhão com 300 kits de painéis por semana. Caso os painéis fossem transportados já montados, seriam necessários 5 caminhões semanais.
O sistema de produção adotado gerou redução no custo de logística de 84,69%, valor economizado de R$ 1.120.500,00, somado a isso temos a redução no tempo e custo de mão de obra aplicada, chegando a 24,98%, valor economizado de R$ 1.102.230,00.
A união das soluções e métodos inovadores aplicados nesse projeto, somados, alcançaram a redução direta no custo de R$ 2.222.730,00.
A instalação da fachada é uma das etapas mais importantes da obra pois, além da fachada ser responsável pelo fechamento da estrutura contra ações externas, chuva, vento, sol, com essa etapa realizada todas as atividades internas podem ser concluídas. A fachada é essencial para a sequência das atividades de acabamento interno e entrega da obra. Caso fosse utilizado o sistema de montagem e instalação tradicional, essa etapa teria duração de 25 meses. Já com o sistema de montagem dentro da obra reduzimos em 73 dias úteis, aproximadamente 4 meses. Com isso, essa etapa foi concluída em 21 meses
Por conta das limitações de transporte, o prazo de instalação se alonga. No caso do sistema tradicional ficaríamos limitados às entregas de 45 painéis por dia, no sistema aplicado tivemos média de produção de 60 painéis por dia.
A execução da fachada era um caminho crítico da obra. Com o sistema adotado alcançamos a redução de 73 dias úteis, aproximadamente 4 meses no prazo de execução da obra.
A mão de obra não sofreu redução, porém tivemos um novo organograma de atividades e setores. Parte da mão de obra de montagem de painéis que estaria na fábrica fora da obra, agora está dentro da obra.
O maior benefício com essa mudança foi a redução no prazo de execução que, por consequência, gerou redução no custo de mão de obra.
Obtivemos a redução no número de caminhões para entrega dos painéis em 84,69%, ou seja, 249 cargas a menos. Esse fator foi muito relevante considerando que a obra está localizada em uma avenida de grande fluxo de carros e pedestres e, dessa forma, reduzimos os transtornos em via pública.
Também obtivemos redução com embalagens de proteção dos materiais, visto que, se os painéis fossem transportados já montados com os vidros e caixa de ACM, a quantidade de material de proteção seria muito maior, para minimizar os riscos de quebras e danos.
Como algumas etapas da produção estão sendo realizadas dentro da obra, duas vantagens referentes a qualidade se destacam: primeiramente, a produção da fachada e esquadrias é acompanhada de perto pela equipe técnica de qualidade até a fase de instalação, com as dúvidas ou problemas resolvidos no momento da montagem, sem o risco de serem instalados inadequadamente.
Outro ganho é com relação a danos nos materiais. Um dos maiores problemas que o método tradicional acarreta são os danos causados pelo transporte dos diversos itens, como painéis inutilizados, janelas, portas que, quando transportados montados dentro de caminhões, são facilmente danificados. Com a produção dentro da obra esse problema é eliminado já que cada kit vem em volume menor, devidamente embalado.
Pode ser aplicada em qualquer obra de médio a grande porte, uma vez que se monta uma fábrica equipada e organizada dentro da obra. Uma obra de médio porte com área de fachada e esquadrias acima de 2000 m² já se torna viável a implantação da fábrica parcial; A área para a montagem da fábrica vai depender do volume e tipo de fachada e esquadrias, a partir de 300 m² já é possível implementar.
É importante que o acompanhamento do fornecedor das esquadrias e fachadas seja realizado desde o começo do projeto, dessa forma toda a área destinada para esse fim já é concebida na fase inicial da obra, além de melhorias executivas já conhecidas que podem ser implementadas para atender essa atividade.
O processo de produção parcial dentro da obra traz diversos ganhos para o projeto. Além da otimização de tempo, o material está dentro da obra, com o acompanhamento direto do cliente, as reduções de danos e perdas nesses materiais é notável, uma vez que a sua movimentação é reduzida.
Devido ao atraso na contratação, tivemos alguns problemas na adaptação do ambiente para implementação da fábrica na obra.
Caso a contratação fosse feita com antecedência, já poderíamos em conjunto com a construtora definir a área para as instalações da fábrica, escolhendo um local mais próximo para descarga de materiais e passagens estratégicas para movimentação e içamento dos painéis.
É importante ter ciência e conhecimento desse sistema de produção de fachada e esquadria dentro da obra, dessa maneira todos os benefícios de redução de tempo e custos podem nascer na concepção do projeto.
Parceiros envolvidos
Consórcio CLN (Luxalum, Central doALumínio, NTC Novatech) |
Luxalum - Engenharia em Fachadas Especiais de Alumínio |
Central do Alumínio – Fachadas Unitizadas e Estruturas de Alumínio |
NTC NovaTech – Fachadas e Esquadrias |
Arqtec – Inovação em Revestimentos |
Neomec – Tecnologia em Mecânica de Precisão |
GE Silicones Momentive |
Schuco – Sistemas de fachadas e Esquadrias.
Luiz Felipe Lucena - CEO Central do Alumínio;
Lucinio Abrantes dos Santos - CEO Luxalum;
Leandro Alves Mota – CEO NTC Novatech;
Mauricio Feiten da Silveira - Engenheiro Coordenador de Obra;
Kerstin Pinz - Engenheira Projetista;
Antônio Carlos Guerreiro dos Santos – Planejamento e Coordenação;
Cristiane Cardoso dos Santos - Engenheira Coordenadora de Obra;
Reginaldo Antônio da Silva - Fiscalização e Gestão de Obra;
Hamilton Batista Gimenis - Encarregado de Instalação;
Luciano Moura de Oliveira - Encarregado de Instalação;
Nivaldo da Costa - Encarregado de Instalação;
Lucinio Abrantes dos Santos - CEO Luxalum;
Leandro Alves Mota – CEO NTC Novatech;
Mauricio Feiten da Silveira - Engenheiro Coordenador de Obra;
Kerstin Pinz - Engenheira Projetista;
Antônio Carlos Guerreiro dos Santos – Planejamento e Coordenação;
Cristiane Cardoso dos Santos - Engenheira Coordenadora de Obra;
Reginaldo Antônio da Silva - Fiscalização e Gestão de Obra;
Hamilton Batista Gimenis - Encarregado de Instalação;
Luciano Moura de Oliveira - Encarregado de Instalação;
Nivaldo da Costa - Encarregado de Instalação;
• https://www.luxalum.com.br/ , http://www.centraldoaluminio.com.br/ , https://www.ntcesquadrias.com.br/