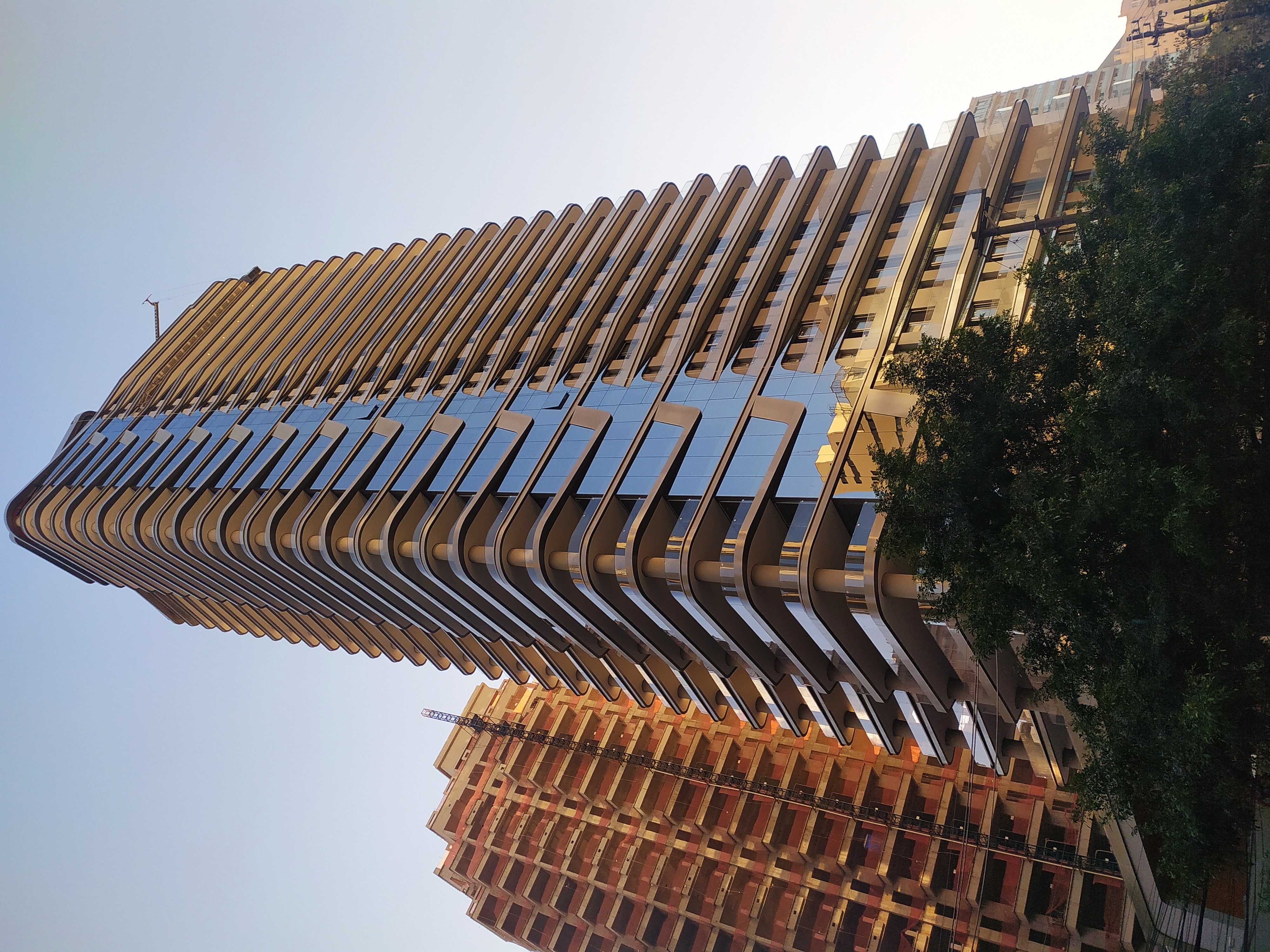
Heritage
A Edificação Residencial fica localizada em São Paulo e conta com mais de 29.300 m² de área construída. O desafio era encontrar fornecedores de peças pré-fabricadas com pintura automotiva, para atender às exigências do projeto arquitetônico, que tinha como referência automóveis modernos, como os da marca Ferrari.
Solução técnica implementada
Tivemos três grandes desafios: encontrar soluções técnicas de projeto para atender à volumetria proposta pelo Incorporador junto ao parceiro internacional Pininfarina, com alta complexidade técnica envolvendo principalmente projetistas de esquadrias e estrutura. Em segundo encontrar fornecedor que tivesse solução construtiva para execução de peças pré-fabricadas e com acabamento estético de pintura automotiva, garantindo o resultado final similar aos automóveis desenhados pela Pininfarina, sendo o mais emblemático a Ferrari. E por fim a solução atender prazo de obra e orçamento previsto inicialmente.
O processo teve início durante o desenvolvimento do projeto envolvendo consultores e fornecedores, com atenção especial para prototipagem. A finalização do projeto aconteceu junto ao início de obra com execução de protótipo 1:1 no canteiro de modo a validar soluções técnicas, estéticas e logística de execução. Foi executado o trecho mais crítico e onde tínhamos a maior interface entre estrutura de concreto, esquadria de alumínio e elemento pré-fabricado. Neste momento fizemos o desenvolvimento com alguns fornecedores que atendiam mercado nacional e internacional e todos puderam visitar o protótipo para finalizar a apresentação de proposta e confirmar se possível atender a parceria, visto que se tratava de uma fachada sem similaridade no Brasil. Definido o parceiro e as estratégias de execução conseguimos avaliar o ganho em produtividade que teríamos trabalhando com o sistema apresentado pela Clamom e ciclo produtivo de seu parceiro, Gatron, na produção das peças. Tivemos pequeno ajuste de dimensões de molduras para otimização de custos, sem prejuízo à volumetria inicial.
Principais resultados obtidos
O ganho de produtividade veio do processo fabril, desde a concepção até a instalação. No momento da instalação, as peças deveriam ser encaixadas, sem nenhum tipo de folga, pois o conceito de juntas era para ser idêntico ao que existe nas peças de um carro. Portanto, foi investido muito trabalho e energia durante o projeto e as antecipações às interferências.
Retrabalho zero. Atendimento do prazo pré-estabelecido. Em custo fixo, um mês de obra representava aproximadamente R$ 500.000,00.
Atendimento aos anseios do Incorporador, empreendimento icônico e com solução de fachada diferenciada, sistema pré-fabricado com redução de geração de resíduos. Desenvolvimento de novos fornecedores e novas soluções construtivas para o mercado imobiliário.
Execução limpa e organizada. Prazos pré-estabelecidos atingidos com êxito. Qualidade final do produto de acordo com as expectativas do incorporador e do escritório de design.
Atenção às folgas necessárias para instalação de elementos pré-fabricados. Buscar padronização estética entre pavimentos para evitar maior quantidade de formas para fabricação dos moldes das peças em sistema composto.
Desenvolvimento dos projetos utilizando metodologia BIM.
Parceiros envolvidos
Cyrela, Clamom, Gatron e ERGs.
Eng. Caio Vasconcelos - Cyrela Construtora;
Arqt. Camila Roma - Cyrela Construtora;
João Mario – Clamom;
Jean Zolet – Gatron;
Lilian Basílio – Gatron;
Fernando Gallego – ERGs – Esquadrias de Alumínio
Arqt. Camila Roma - Cyrela Construtora;
João Mario – Clamom;
Jean Zolet – Gatron;
Lilian Basílio – Gatron;
Fernando Gallego – ERGs – Esquadrias de Alumínio
https://www.cyrela.com.br , http://clamom.com.br , https://www.gatron.com.br/ , https://www.metropoles.com/dino/compositos-viabilizam-primeiro-projeto-arquitetonico-da-pininfarina-no-brasil , https://www.compositesworld.com/articles/composites-meet-precision-weight-goals-for-complex-facade-design ,,